Syntegon Launches New MLD Advanced for RTU Syringes
hits:144 Date:04/15/25
* 100 percent IPC enables flexible redosing with maximum product yield
* Gentle processing of up to 400 syringes per minute
* Combination of proven technologies ensures fast availability and low risk
Waiblingen (Germany), April 14, 2025. Following the first virtual presentation at Interphex, Syntegon is now introducing its new filling machine for ready-to-use (RTU) nested syringes to the market. The MLD Advanced meets the increasing requirements of pharmaceutical manufacturers for high output with 100 percent in-process control (IPC). “Especially with high-value medicines, it is essential that each drop is filled and weighed optimally,” explains Markus Burkert, Product Manager at Syntegon. “That's why we have combined the MLD platform, which was previously used primarily for cartridges and vials, with our technologies for syringe filling.”
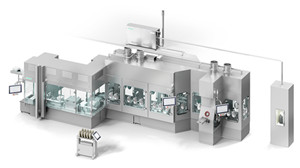 |
The new MLD Advanced from Syntegon meets the increasing demands of pharmaceutical manufacturers for high-output filling solutions for RTU syringes. |
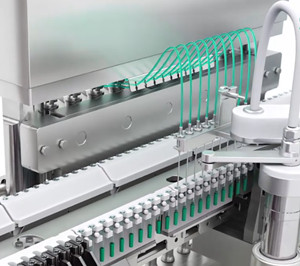 |
The filling needles, which are mounted on the Pharma Handling Unit, enable flexible redosing if required. Thanks to 100 percent in-process control (IPC), the filling weight is controlled precisely. |
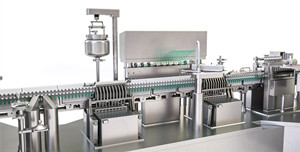 |
The first MLD Advanced will soon be ensuring gentle processing and filling of RTU syringes with 100 percent IPC at a European pharmaceutical manufacturer. |
An innovative combination of proven technologies
The automatic bag and tub openers, well-known from many syringe lines, use no-touch transfer to ensure the aseptic transfer of the syringes into the filling area. The Pharma Handling Unit developed by Syntegon denests the syringes automatically without glass-to-glass contact and places the containers into the pitch adjustment station. Here, the syringes are moved into the machine pitch and then placed in the clips of the machine transport. “This unique clip system is the first key feature we adopted for syringe applications from the cartridge line,” Markus Burkert explains. “The special circulating transport system ensures smooth transportation and is therefore ideal for RTU syringes, as well as vials and cartridges.”
The empty syringes are weighed using 100 percent IPC, before they are transferred to the filling station. The subsequent filling and stoppering process is based on the proven FXS series for syringes: the filling needles are mounted on the Pharma Handling Unit and allow for flexible redosing if required. Thanks to IPC, the filling weight is controlled precisely. “In addition to minimizing product loss, an important focus is on providing documented proof about the weighing of each container. This gives manufacturers the certainty that all containers have been filled correctly,” explains Klaus Ullherr, Senior Product Manager at Syntegon. After stopper insertion via vacuum or vent tube, the containers are returned by the circulating transport system and gently placed in the nests by the Pharma Handling Unit. “This way, we can offer our customers a seamless process for their pre-sterilized syringes from a single source,” says Klaus Ullherr.
First customer order already placed
Customers benefit from this innovative combination of proven technologies in several ways: in addition to achieving an output of up to 400 syringes per minute, they also receive safe and proven processes. “By using tried and tested technologies, the machine is available quickly, and the risk is significantly reduced,” Markus Burkert underlines. The first customer is already convinced: the first MLD Advanced will soon be ensuring gentle processing and filling of RTU syringes with 100 percent IPC at a European pharmaceutical manufacturer.
About Syntegon
Syntegon is a strategic partner for pharmaceutical and food companies. 6,300 employees worldwide support them with seamless processes, innovative technologies, and sustainable solutions. Syntegon’s integrated lines and system solutions enable the flexible, reliable, safe, and high-quality production and packaging of pharmaceuticals and food. Headquartered in the Stuttgart region, Germany, Syntegon looks back on more than 160 years of experience. In 2023, the company achieved annual sales of 1.5 billion euros. With a global presence of more than 35 locations in almost 20 countries and a comprehensive service portfolio, Syntegon provides seamless processes for its customers. The company’s 1,400 employees in research and development work on leading technologies every day – 2,100 patents and patent applications are proof of the processing and packaging expert’s innovative strength. By providing sustainable solutions, Syntegon enables the industry to switch to alternative packaging solutions and resource-conserving production processes. www.syntegon.com.
|